摘 要:以白云石为载体制备的Ni基催化剂对松木粉在700℃下气化产生的焦油进行了催化裂解实验研究,并与重油裂解催化剂进行了对比。结果表明:石油化工重油裂解催化剂对生物质气化焦油具有一定的催化裂解作用;Ni的掺人方式和催化剂的煅烧温度对催化剂的性能具有显著的影响。以100~120目白云石粉为载体,900℃下煅烧的N基催化剂在700℃下焦油裂解对H2和CIL具有很好的选择性(H2为78.3%,H2+CO为92.3%,CH4为2.3%);100h老化实验显示H2/CO随催化剂活性降低而逐渐减小。
关量词:生物质;焦油;催化裂解
0 引 言
生物质气化和间接液化是生物质能高品位利用发展最迅速最实用的技术之一。气化的目标是得到尽可能多的合成气体产物,特别是高的H2含量和低的CH4含量。但在气化过程中,焦油是不可避免的副产物,焦油在高温时呈气态与合成气体完全混合,低温时(低于200℃)凝结为液态,其分离和处理极为困难,在合成气需要降温利用的情况下,问题更加突出。裂解净化技术是将生物质在气化过程中所产生的焦油裂解为可利用的一次性气体,催化裂解可降低裂解温度,具有裂解产物的选择性,既提高气化效率,又提高了合成气的利用价值,对发展和推广生物质高品位利用技术具有决定性意义。
1 实验部分
1.1 实验仪器
实验是在WFS—3010型常压微型反应装置上进行的,装置流程如图1所示。
该装置催化剂装填量为5mL,有两路气体稳压、质量流量计控制的物料气路,一路液体流路人口,程序升温,温控仪为SHINKO FCR—13A。反应器为石英固定床,可排除金属反应器在高温条件下对催化剂的干扰。SHIMADZU GC—20B气相色谱分析裂解气体成分、A&D HM—200电子天秤称重、THERMO ISIR1000全谱直读电感耦合等离子体发射光谱仪分析催化剂成分、ELEMENTAR vario ELCHNOS分析仪分析松木粉元素、WGR—l氧弹测量松木粉高位热值。
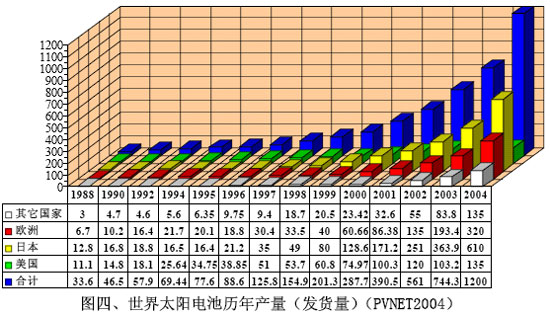
1.2 实验操作
1.2.1 催化剂制备
将硝酸镍晶体溶人蒸馏水中配成溶液,将白云石粉碎成一定粒度与硝酸镍溶液混合,加人粘合剂,干燥、炬烧、压片成型、粉碎过筛,成品催化剂的元素分析如表1所示。
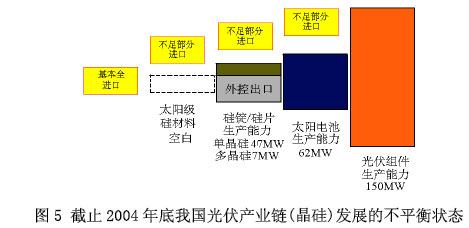
1.2.2 实验过程
经干燥的松木粉装入气化器中在700℃气化,由焦油收集管收集产生的焦油。将微反应装置设定升温参数,使反应器温度从室温以40℃/min的升温速率升到700℃,将焦油收集管插入装填好催化剂的石英反应器中,气化的焦油由载气N2携带通过催化剂床层裂解。裂解后剩余的焦油经冷凝后由焦油收集器收集,裂解气体用气相色谱分析,各相关成分由电子天秤称重。
[NextPage]
2 结果与讨论
2.1 原料化学物理性质及气化特性
实验所用原料为松木粉,化学分析特性如表2所示。松木粉的元素组成中O的含量高,C/O比值接近于1:1,这是生物质作为碳水化合物的共性。H的含量在7~8%之间。在气化的过程中,除生成可燃气体外,还会生成水蒸汽,在高温的条件下发生水煤气变换反应生成H2。松木粉中基本没有S的存在,不会对环境造成危害。大部分焦油成分,能与水蒸汽发生化学反应,生成CO和H2等可燃气体,从而减少在催化剂表面的积炭。松木粉气化的温度和气相停留时间对产生焦油的数量和成分有较大的影响,气化温度高,可燃气中焦油明显减少。实验表明:松木粉气化过程中的气相停留时间太短,收集的焦油中含有大量的水;适当延长气相停留时间,焦油和水的含量明显降低,部分焦油与水蒸汽在高温下发生了化学反应。
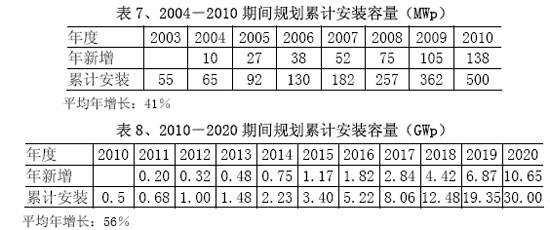
[NextPage]
2.2 Ni基催化剂与其它催化剂的催化性能
在WFS—3010型常压微型反应装置上控制相同的升温条件和载气流量,对几种催化剂的催化性能进行了对比,裂解后气体成分对比如图2所示,焦油裂解率分别为:无催化剂热裂解(31%);白云石催化剂(59%)镍基催化剂(99%);重油裂解催化剂(95%)。生物质焦油催化裂解的原理与石油的催化裂解相似。由图2知,石油化工重油裂解催化剂对生物质气化焦油也具有催化裂解作用,在700℃下焦油裂解率达95%。但裂解产物中C02和CH4的含量较高。综合考虑裂解气体中H2、CO和CH4的含量,在700℃下几种催化剂的催化性能为:Ni基>重油裂解>白云石>热裂解。白云石需在高温下才有较高的焦油裂解率,为减少裂解气体中C02的含量,白云石在使用前必须在高温下(>900℃)燃烧处理。热裂解需要很高的温度(1000~1200℃),在700℃下裂解率很低。自制的Ni基催化剂显示出良好的催化裂解性能,产物中H2含量很高,绝大部分为合成气(H2+CO),且CH4的含量较低(<0.1%),焦油裂解率达99%以上。因此应对照基催化剂的制备工艺进行优化,以保证在相对低温下良好的催化裂解性能的前提下,降低制备成本和延长使用寿命。
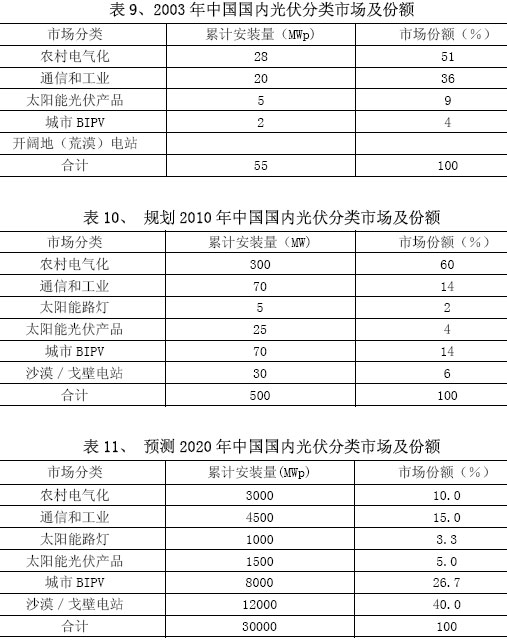
2.3 刚基催化剂制备工艺优化
制备的Ni基催化剂采用白云石为载体,Ni为活性组分。白云石作载体,成本低且其本身就有一定的催化能力。白云石需粉碎成一定的粒度,以获得较大的比表面积。为使Ni的分布均匀和防止Ni的损失,在制备过程中,需在一定的真空环境下边加热边蒸发干燥,以排出催化剂微孔内的空气,使镍离子尽可能多地进入微孔内。因白云石较脆,容易粉化,压片的压力需保证制备的催化剂在高温下具有一定的强度,本实验压力为15MP。在不同的载体粒度下Ni基催化剂的催化性能如图3所示。随着白云石粒度的降低,H2的含量先增加后降低出现一个最大值;而CO的含量正好相反,在同一粒度范围内出现一个最小值。在此粒度范围内H2与CO的总含量也达到最大值,而CH4则达到最低含量。由此说明,在制备催化剂的过程中,最佳的白云石粒度应在100~120目的范围内。粒度过大,则催化剂的比表面积小,催化性能差;粒度过小,则影响催化剂的微孔结构。焦油的成分非常复杂,大部分是苯的衍生物及多环芳烃,载体粒度太小,不利于大分子进入微孔内与活性中心接触,从而催化性能降低。催化剂的燃烧温度对其催化性能具有十分显著的影响。如图4所示,随着温度的升高,H2的含量逐渐升高,CO和CH4的含量逐渐降低。当温度超过900℃时,变化的趋势逐渐乎缓,即再升高温度对催化剂的催化裂解性能无明显促进意义。实验表明,燃烧温度低于800℃时,所得的催化剂稳定性差,裂解的气体中含有大量的C02。C02的产生是由于在催化剂燃烧后残留的碳酸盐在催化反应过程中热分解所致。因此合适的燃烧温度为900℃,高于此温度会大大增加催化剂的性价比,低于此温度会影响催化剂的使用寿命。
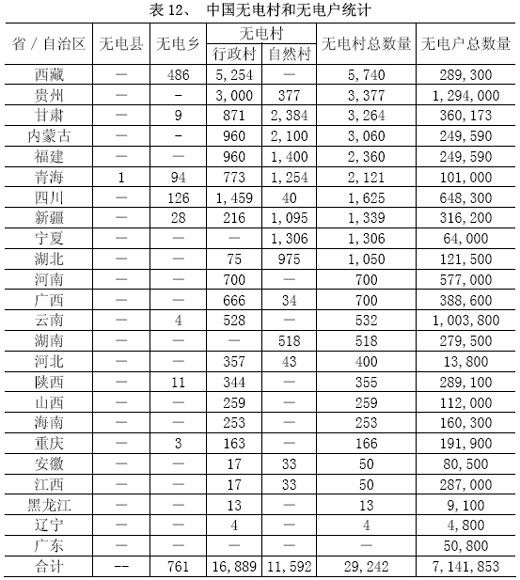
2.4 催化剂老化性能
在700℃下焦油通过催化剂床层进行连续的催化裂解反应,通过分析裂解气体组成的变化来考察其老化性能。如图5所示,制备的N基催化剂在开始的40h内保持良好的活性和稳定性,随着反应时间的增加,H2的含量逐渐减少而CO的含量逐渐增加。原因是催化剂床层的上层催化剂表面积炭,活性降低,这一点由裂解气体中H2含量大幅度降低以及CO、C02和CH4的大幅度增加得到了证实。在反应时间达到75h,H2含量降低到48%(扣除载气N2)时,进行反应器内原位再生,再生气氛为含有水蒸汽的空气,通过控制再生气氛流量和温升条件,其活性基本恢复。在整个实验过程中CO和H2的总含量维持在80~90%范围内,表明随着催化剂活性的降低,H2/C0的含量比逐渐变化,但总量基本维持不变。
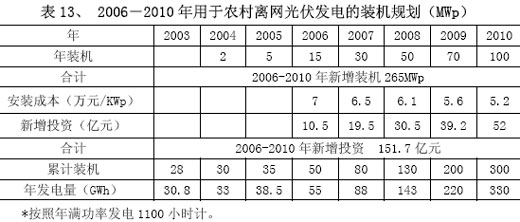
3 结论
1)石油化工工业重油裂解催化剂对生物质焦油具有催化作用,但其效果次于Ni基催化剂,且价格昂贵,不适合直接在生物质气化工艺中应用。
2)100~120目的白云石粉为载体,900℃下燃烧的Ni基催化剂在700℃下焦油裂解对比和CH4具有很好的选择性(H2为78.3%,H2+CO为92.3%,CH4为2.3%)。
3)积炭是造成催化剂失活的主要原因,随着催化剂活性的降低,H2/C0逐渐减小,但总量基本维持不变。